X-RAY HELPS LEADING MEAT PROCESSOR TO STRIKE THE RIGHT BALANCE BETWEEN FOOD SAFETY AND PRODUCT INTEGRITY
Kepak Group is a family-owned Irish company, enjoying a strong reputation for sustainable food production. The group processes a broad range of fresh and value added meat products, serving the international foodservice and retail markets with prime cuts of meat, on-trend foodservice solutions and market leading consumer brands.
Kepak’s portfolio of market leading brands include Rustlers, Big Al’s, Feasters, Stript Snacks, and Celtic Beef. Kepak employs over 4,500 people across 12 manufacturing facilities throughout Ireland and the UK, and has sales offices in Europe, the US, Asia and Africa.
The Challenge - do more in the same space
In addition to providing a foodservice offering, Kepak’s Kirkham - UK site mainly manufactures a range of Microwavable Burgers and Hot Sandwiches that come in clear 100% recyclable packs, with additions such as cheese and sauce. Kepak Kirkham produces Rustlers – a Top 100 Brand in the UK and Europe’s No.1 brand of micro snacks. With the brand built around taste, convenience and quality, operating to world class food safety standards is a major area of focus. This focus results in the site consistently achieving the highest grades in food safety and quality audits.
All of the site’s 8 processing lines used an ageing mix of metal detectors and checkweighers, which were not suitable to detect softer contaminants such as bones, as well as ensuring that a sauce sachet and cheese slice were correctly placed in the packs. Kepak wanted to increase their detection capabilities, but also continue to weigh their products and check product integrity, all within a smaller footprint.
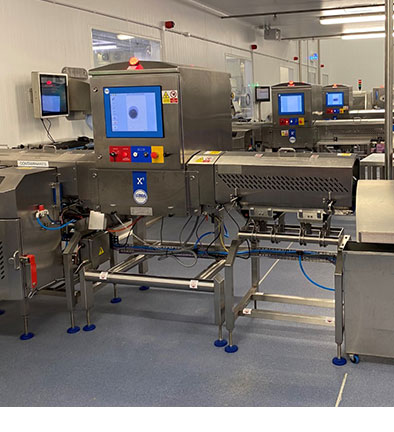
The Opportunity
Due to the complexities presented by the final ‘on-the-go’ burger product, it was decided that each line should have a new X-ray machine, to provide best-in-class metal contaminant detection and an equally impressive capability for detecting softer contaminants such as bone, ceramic and glass. In addition X-ray would check the product’s integrity, plus product weight and volume to a 3g tolerance. The X-ray solution also needed to deliver a line throughput of 100 packs/minute to meet production requirements.
Following extensive consultation, Loma was appointed to supply the Kirkham site with 8 of their market-leading, compact X5 Space Saver X-ray units, offering detection of various contaminants and enabling easy line integration.
The Solution - X-ray to the rescue
Loma installed 8 X5 Space Saver X-ray units into Kepak’s production lines. In providing first-class CCP protection in a modest footprint, they successfully met Kepak’s exacting quality requirements for contaminant and product integrity checks.
“We had very high expectations of Loma’s X-ray machines which, given the nature of our product types, needed some detailed scoping to get the equipment to function perfectly. Once that had been achieved, we were delighted with the end result.
During installation, Loma’s technical team were passionate in ensuring that the X-rays were performing at their best - to that end I can’t be happier. I have 100% confidence in Loma’s X-ray technology.”
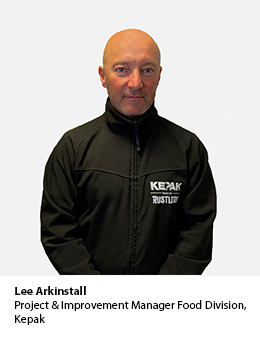
Kepak’s Experience of the X5 Space Saver
Design Benefits
- Provides the very best detection levels – 0.4mm for very small metal contaminants and 0.8mm to 1.6mm to find softer contaminants.
- First-class CCP protection in the smallest footprint, with line length of just 1000mm.
- Built for 24/7 operation.
- Perfect for products up to 180mm in height.
- Ability to easily switch products via the machine’s set-up wizard.
- Network connectivity for remote product changeover and network data sharing.
Production Benefits
- Upgrading from metal detection to X-ray means Kepak can now detect more contaminants.
- Achieves a throughput of 100 packs/min.
- X-ray meets stringent quality and Code of Practice requirements.
- Pack component integrity checks ensure product weight and volume down to a 3g tolerance.
Share this Case Study
To share the full story on how the CW3 RUN-WET® helped Bakkavor download the PDF below.
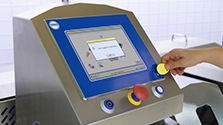
CW3 RUN-WET® Metal Detector & Checkweigher
Working within a harsh washdown environment? See how RUN-WET can make your cleaning regime quicker and easier.
X-ray inspection FAQ's
Understand more about X-ray inspection, how it compares to metal detection and what it can do for your production.
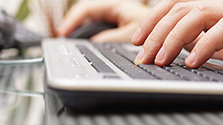
To see how the X5 Space Saver can help your application or for general information Call +44 (0) 1252 893300 or email on the link below.
Share this Case Study
To share the full story on how the X5 Space Saver helped Kepak download the PDF below.
If you need more information contact us on 01252 893 300 or request expert advice
If you need some advice, please feel free to call us or request an expert, click the button and fill out the form.
We have a UK based customer service team ready to help and keep your food safe.