Why having functional fail-safes improve food safety
16 Feb 2021
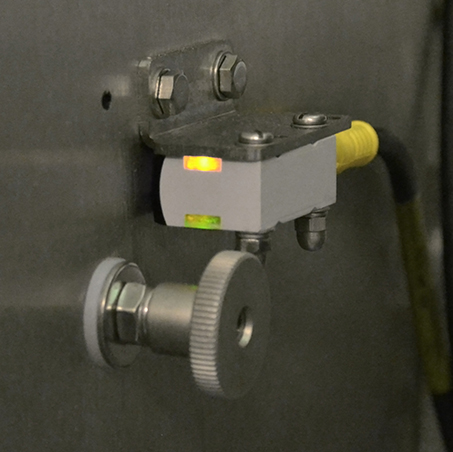
The importance of food safety
Food manufacturers play an essential role in food controls to ensure meaningful protection against real and important safety hazards.
Safety for many in the food industry is a top priority as product recalls and consumer dissatisfaction can be highly detrimental to both manufacturers and retailers, meaning best avoided at all costs. Companies managing safety risks do so by having in place suitable safety policies, processes and machinery.
How can food safety go wrong?
Even with today’s regulations that factories and retailers adhere to, things can still go wrong within food manufacturing and safety can be compromised. Factories are often busy with a big focus on achieving production output and despite the manufacturer’s good intentions, there can be a risk that products worthy of being rejected get overlooked.
Is safety all about the consumer?
Safety concerns do not just relate to the consumer and can also relate to the production line machine operators in the event of insufficient machinery protection, that could potentially harm the user. Fast moving machinery can be very unforgiving and would potentially cause serious injury if body contact were to be made in error.
Plus, if a contaminant like metal from a broken production machine were to find its way into the product being produced, then damage could occur to other machinery on the production line. These are just some of the safety issues that may occur, but fortunately can be detected and stopped at critical control points with functional fail-safe measures.
How has the presence of safety controls changed over time?
The last twenty years have seen regulations tighten-up, with many retailers taking a keen interest in improving safety and developing their own Codes of Practice (COP). These are the manufacturing standards that their suppliers must adhere to if they want to do business and be present in the market through the specific retailer. COP’s are good news for the consumer, as they mean they are better protected as the supplier strives to mitigate safety risks in the factory.
To help with the detection of contamination issues and ensure corrective measures are taken, technology has been further developed to offer smart and reliable solutions. Not only is there technology like X-ray that literally looks inside a product to find a contaminant such as metal, glass, dense plastic or stones, but modern machines include additional machine functionality that double checks the integrity of the inspection system, often used as a Critical Control Point (CCP). These devices are designed to fail-safe in the event of a problem and includes functionality such as a sensor to detect the failure of the compressed air supply.
If no air was present, then the reject mechanism itself could not actuate and remove the rejected product from line – it would simply carry on where it would be boxed and distributed to the retailer. These devices also provide a secondary back-up to ensure manufacturing working practices are operating correctly.
Fail-safe functionality is required by the retailers
With food safety very much a concern for all manufacturers, many machines along the production line have these fail-safe features. With LOMA Metal Detector, X-ray inspection and Checkweighing systems, some of the most common devices are as follows.
All of these fail-safe devices help make a manufacturer’s operation commercially viable and ethical, plus keep everyone safe. Examples include:
- Sensors to count and confirm that a pack has been successfully rejected into the reject bin.
- Confirmation that a reject bin is actually closed so that the conveyor can be operated.
- Locked reject bins so only authorized personnel can handle rejected product.
- Sensors to detect whether reject bins are full.
- The latest system security with multi-level user access management and passwords to ensure controlled access.
- Detection of compressed air supply failure.
- Conveyor guards to prevent operators tampering with the product and risk of injury once it has passed the CCP.
- System reporting that documents products rejected for managing the line and audit purposes.
Who benefits from these fail-safes
Everyone benefits from fail-safes being in place at CCPs as the supplier strives to mitigate safety issues in the factory.
In the unfortunate occurrence when a safety issue happens, these fail-safe devices are necessary and an industry best practice to help demonstrate a zero-tolerance attitude to foreign body contamination and are there for the ultimate protection of safety. With these measures in place, the result is the best possible product integrity so both retailer and customer safety expectations are met, and no harm done.
Fail-safe featuring at CCPs are not just important for today, but in the future to ensure manufactures meet retailer’s Codes of Practice and any potential new business opportunities are secured.
LOMA SYSTEMS has decades of experience working with retailers in helping develop meaningful Codes of Practice. With this knowledge, LOMA can offer consultancy on suitable functionality and the right fail-safe solutions to enable manufacturers to be compliant with the various retailer Codes of Practice.