What reject system is right for my application?
23 May 2019
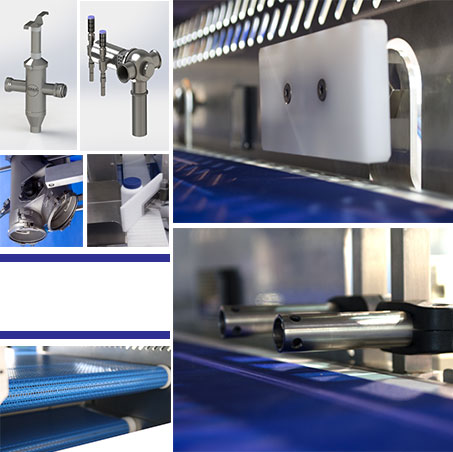
What Reject System is best for me?
In addition to a wide range of inspection equipment, Loma Systems® offers a variety of reject mechanisms for your application. A reject mechanism will quickly remove any contaminated product from the production line to help producers meet safety regulations and maintain uptime.
With an assortment of reject options available, it may be confusing to know which is right for each application. The type of reject mechanism needed is dependent upon a variety of factors including the type of inspection system it is paired with and the line speed, plus specific product details like type, packaging, size and weight. Here is a breakdown of some of the standard rejects:
Reject systems for conveyorized operations
Stop on Detect
The simplest and most economical reject option is the stop on detect (SOD). The SOD reject causes the conveyor to stop once a contaminant is detected so the product can be removed from the line. It is perfect for heavy or awkward shaped products as well as continuous/bulk product. The stop on detect is also ideal for production lines with limited space as it allows for the shortest conveyor lengths. This reject is suitable for individual packs up to 60kg on the belt at any one time.
Air Blast
The air blast reject is a nozzle that is attached to the outfeed conveyor and provides a blast of air to remove the contaminated product off the conveyor belt and into a reject bin. This allows the line to continuously run while packages are rejected so there is no disruption in production. This reject type is ideal for lightweight, packaged products such as granola bars or bags of potato chips. This reject Is not recommended for open packages or breakable packaging that could spill or shatter when rejected. The pack weight for this reject is up to 0.8kg.
Pusher
For heavier, wrapped products in rigid packaging, a pusher reject mechanism is recommended. This reject consists of a pusher blade attached to an arm that will push any contaminated product off the conveyor belt and into a reject bin. The pusher can either come from the side or from overhead depending what products are being run on the line. This reject isn’t suitable for poly-bagged products unless a reject brush strip is fitted to the mechanism that prevents the bags from becoming trapped under the pusher blade. The maximum weight range for both the side and overhead pushers is 10kg. A heavy-duty pusher option is also available for any product that weighs up to 50kg and has a max pack rate of 15ppm.
Carriage Retract Band
The carriage retract band reject is a retracting conveyor where the belt retracts toward the inspection system once a contaminated product is detected. This allows for the contaminated product to fall into a reject bin. This mechanism is ideal for continuous or loose product, products in parallel lanes across the belt, polybags or sachets. The carriage retract band has a maximum individual pack weight of 5 kg.
Flap
The flap reject is ideal for bulk/loose product where the outfeed conveyor is lower than the inspection system conveyor. Product freely falls onto the outfeed conveyor as it is inspected and, if a contaminant is detected, a flap will pivot to direct the contaminated product into a reject bin.
Plough/Diverter
The plough/diverter reject is ideal for fragile and bottled products with low pack rates. This reject will divert the contaminated product typically sideways into a reject tray, then reopen to continue allowing non-contaminated products to move along the production line. The individual weight for this reject is up to 1kg.
Power Declining Belt
The power declining belt is most common for checkweighing applications. When an over/underweight product is detected, the outfeed belt pivots in a downward motion to drop the affected product into a reject bin. This reject is suitable for individual packs up to 5kg with a maximum height of 100mm.
Reject options for Pipeline applications
Piston Valves
This reject pushes out the contaminated product via a piston mechanism as it moves through the pipe to allow for continuous product flow. Once a contaminant is detected, the piston operates on a timer diverting the product flow briefly to a reject port ensuring that the portion of the product flow containing the contaminant is successfully removed from production. These valves can be used for inspecting meat slurries, soups, sauces etc.
Rotary Valve
Rotary valves consist of the valve body that is connected to a pneumatic actuator and is capable of cutting through muscle protein. When a contaminant is detected, air is supplied to the valve actuator, which then causes the ball to rotate to open the reject pipe and divert the contaminant before rotating back into place for continuous product flow. These valves are typically used for inspecting whole muscle protein.
Maximum flow rates for all pipeline reject mechanisms is dependent upon the size of the pipe needed for production.
Reject options for Freefall applications
Cow Bell
For gravity-fed, unpackaged, free flowing products such as dried foods, cereals and grains, a cow bell reject would be one option. This reject allows product to flow through a pipe, but once a contaminant is detected, a pivoted swinging chute diverter will temporarily redirect the product flow to remove the contaminated product.
Sealed Valve
For fine particles or powder products, a sealed valve reject is recommended. With this mechanism, a sealed flap moves briefly into the gravity-fed product flow when a contaminant is detected, which diverts it to a reject bin. The seal on the flap helps keep dust from escaping into the environment if the reject bin is also sealed.
Maximum flow rates for reject mechanisms for free-fall applications is also dependent upon the size of the pipe needed for the application.
Conclusion
In conclusion, it is not only necessary to have the proper inspection system for your application, but it is also important to ensure that products with contaminants are removed appropriately to maintain safety standards and minimize downtime. There are a lot of factors including product type, size, shape, weight and belt speed that should all be taken into consideration when choosing the correct reject for your LOMA inspection system.