Keeping you Inspecting and Operational
15 May 2020
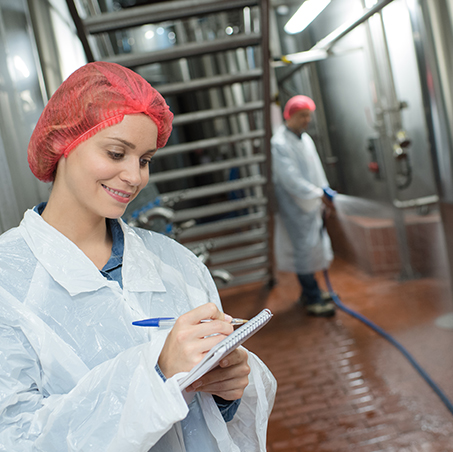
With the added pressure of Covid-19, many manufacturing businesses have had to re-prioritise their procedures and practices. With these challenges, it is as critical as ever before to not neglect your inspection equipment.
Whether your production line has seen an increase or decrease in demand, make sure you are keeping your inspection solution primed and always ready to perform with maximum effectiveness. Neglecting this key CCP (Critical Control Point) could result in bigger issues such as malfunction or bacterial contamination.
Here are some simple actions to keep your inspection equipment problem free:
Regular testing of detection sensitivities
Don’t forget to carry out regular testing, clearly documenting it so you are confident the equipment is detecting to the specified sensitivities. Testing should take place at the start of each shift, between each change of product and carried out at least hourly. (sometimes more depending on your product and procedures)
Intervals between tests need to be short enough that if a fault is found, then the necessary action can be taken and products affected can easily be identified, recalled and retested before leaving the premises. If your company is a private label manufacturer, then ensure you agree upon any variation you make to testing procedures, in writing, with your customer.
To help facilitate effective testing, Loma’s PVS (Performance Validation System) feature automatically prompts the operator to carry out the required test at a pre-set interval. A PVS test involves passing test packs , along with the test pieces, through the equipment to validate that the machine is effectively detecting to the specified detection levels. Please note it is important to make fresh test packs at a frequency that reflects the nature, durability and shelf life of the product concerned. If you use ‘stale’ test packs, they will not reflect the same properties as the products which the system is inspecting.
Check all fail safes are working.
As part of the testing, it is also important to check that all fail safe mechanisms like bin full alerts and rejects systems are all operating correctly. If you are unsure how to check your fail safes then contact Loma for advice.
Regular maintenance and service
Whatever pressures you are under, it is important to plan maintenance so that wear and tear can be remedied before defects occur. If your line is busy then try and schedule for a time when the equipment is idle. Maintenance and service should be carried out by the original manufacturer or your engineers if they have been trained accordingly.
At Loma we are 100% committed to supporting you and our team of service engineers are here to help all our customers with remote diagnostics and on-site visits to resolve any issues or provide routine maintenance. You can book a service appointment or report a performance issue.
Cleaning
Your exact cleaning regime is dependant on whether a high-care or low-care area, but nevertheless regular cleaning is important to keep all components free of debris so the machine delivers total reliability and optimum performance. So be sure to keep up your regular cleaning regime to protect from bacterial contamination and to keep all components clean.
When cleaning inspection equipment in food factories, there is no one set cleaning regime to follow. A high-care versus low-care area of a factory will have very different needs, high-care is often wet or dusty, with greater bacterial risk, whereas a low-care area is likely to require less work to keep it clean.
To establish and complete the most suitable cleaning regime for your inspection equipment, particularly for high-care production areas, specialist cleaning companies are available to provide professional guidance. Such experts are critical in advising how best to manage bacterial risks, and with bugs often becoming resilient to cleaning chemicals, they will often recommend rotating different chemicals to help preventing contamination.
In addition to getting expert advice, there are some basic ‘must-follow’ steps when cleaning your inspection equipment:
Read instructions - Always follow the cleaning chemical manufacturer’s instructions.
Concentration levels - Do not exceed the cleaning chemical manufacturer’s stipulated cleaning chemical concentration levels, as an incorrect ratio might damage your equipment.
Contact time - Never exceed the time you leave cleaning product in contact with the inspection equipment, as it might be detrimental to the cleaning results, plus harmful to the equipment.
Rinsing - The equipment requires a thorough rinsing with cold water to remove all cleaning products. There are 5-stages of rinsing: pre-rinse; detergent rise, rinse, disinfectant rinse, final rinse.
Drying - Where possible, dry the equipment prior to recommencing production as this prevents the long-term pooling of water that could present a corrosion risk.
Swab - Before recommencing production, it is recommended doing a swab test to ensure the required level of hygiene is maintained and is confirmed as bacteria free.
Spare Parts Kit
Investing in one of LOMA’s comprehensive Spare Part Kits consisting of the commonly used critical spare parts including: transport belts, timing pulleys, loadcell etc. is always recommended. Spare Part Kits are designed to include items that are commonly replaced due to wear that can be changed by internal engineering staff if needed. Loma can also provide a bespoke option to enable other items to be added to the kit to meet your specific needs.
Need support or spare parts for your inspection product?