Food contamination foiled again
15 Oct 2014
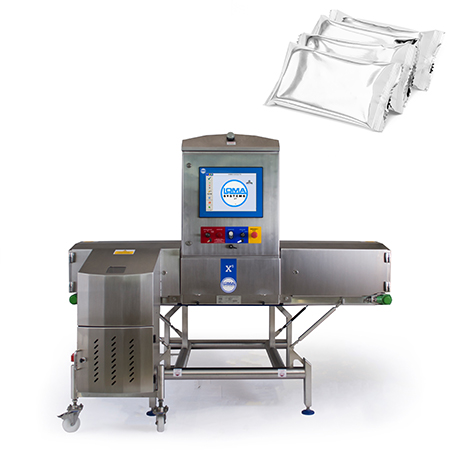
An increase in the flexible packaging market presents new challenges in relation to food inspection equipment. What is the best solution, metal detection or X-ray inspection?
Adoption of foil laminates in the flexible packaging market is leading the freshness food agenda, delivering a longer shelf-life and changing how consumers interact with products. The use of foil in packaging also presents new challenges in relation to food inspection equipment. Loma Systems highlights the benefit of xray detection versus traditional metal detectors. Recent market research on the packaging industry, valued the European converted flexible packaging market at £12.1 billion in 2012, reporting a 2.1% growth in consumption. Confectionery, fresh and processed meat and poultry, cheese and dairy, coffee, dried foods and cereals, and baked goods all experienced sales exceeding €1 billion.
One area anticipating explosive growth in the next decade is aluminium foil packaging - about 75 percent of which is used for food. According to the European Aluminium Foil Association’s 2013 report, thinner gages of aluminium foil, used mainly for flexible packaging and household foils, led the market in the second quarter, with a rise of 2.3% compared to the previous year. This indicates that consumption of aluminium foil in food applications is experiencing stronger gains than the overall flexible packaging market.
Aluminium foil delivers prolonged shelf life to valuable foodstuffs, as it provides a barrier against air and light. What’s more, foil can have a bright or metallic finish, and can be lacquered, printed or embossed. The ability to add high-end graphics can be more striking in design and appealing to consumers. Plus, when a metallic finish is used, consumers will often perceive it to be a premium quality brand. It’s also much lighter in weight and is more compact compared to rigid packaging. As a result, products take up less warehouse storage and retail space. And because more products can be loaded onto transportation vehicles, this helps to cut carbon emissions in the distribution supply chain.
Putting the growth of foil into context, Neil Farmer, independent consultant and spokesperson for the packaging sector, says: “The use of glass packaging is beginning to level off, with European growth at less than 2%, compared with flexible packaging at 4%.” Neil also notes that there is a marked trend in the reduction of the number of flexible packaging layers being used. “This is not just because of packaging reduction initiatives by many leading FMCG producers, but also because of improved barrier performance and developments in barrier resins and materials.” One example is the introduction of styrene-acrylonitrile (SAN), which is helping to combat the issue of foil fracturing caused by creases.
Neil adds: "Generally consumers want packaging that keeps products in good condition. For foodstuffs, they want products that are fresh and ready to be eaten. Ultimately, they seek longer shelf life, product security and value for money.”
Given the wider choice of new design concepts - incorporating pouches, films and laminate foils - manufacturers need to carefully consider their future inspection requirements. Many have successfully used metal detection systems for decades to ensure food is free of metal contaminants. The growing use of foil in food packaging means Loma Systems is seeing a clear migration towards x-ray systems to ensure food safety remains of the highest standard.
“For retailers and consumers, food safety is of upmost importance,” says Tony Bryant, UK Sales Manager at Loma Systems, the company that installs detection systems in many of the world’s largest food companies.
“This is when x-ray detection systems come into their own. Generally speaking, metal-based packaging is not always compatible with metal detectors. However, X-ray systems have no problem seeing right through these packages and are able to detect very small contaminants inside, ranging from metal fragments, glass, stones, bone and ceramic. Plus, they are suited to food producers that handle a variety of different packaging.”
Contaminants aside, another benefit of x-ray detection is the technology’s ability to spot missing products, imperfections or low fills. Take the Loma X5 range. “As an x-ray system, it can literally see inside the container of a ready meal or box of chocolates, alerting operators if product is missing or broken,” explains Tony. “What’s more, today’s new generation systems can handle product density variations and can memorise up to 200 products. Complying with retailer’s Codes of Practice, they are as robust and reliable as conventional metal detectors.”
Food producers and packers face all types of operational risks, and their ability to demonstrate due diligence to retailers and consumers in relation to contaminant detection remains paramount. Although there are many viable detection systems on the market, Loma Systems remains one of the few to offer the full range. Requirements vary depending on individual risks. With all of these developments in food packaging, it’s worth asking the question: is my inspection equipment meeting my packaging needs?