Ten Things to Consider When Selecting a Metal Detector
12 Aug 2020
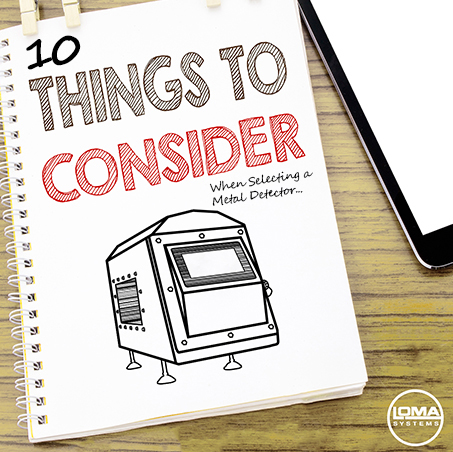
When selecting a metal detector, you want to make the right choice for your business and ensure when installed it maximises the return on the investment.
Metal detector technology has been around since 1881 and so is reassuringly tried and tested in identifying metal contaminants, but here are some useful things to consider when investing in this technology for your production line.
- Application Need. It is important to select the right metal detector set-up to suit your application need. Whilst many food products can operate with a standard metal detector head fitted to a conveyor system, there are other configurations which may be better suited for production lines managing pumped product like jam and checking free-fall products such as powders and granules.
- Cleaning Requirements. If the metal detector is operating in a high-care environment, then it must have the ability to withstand harsh high-pressure and high-temperature cleaning regimes. It is important to consider a system that is completely IP69 rated to reduce the risk of failure and subsequent production downtime.
- Aperture & Product Size. Aperture size of the metal detector head versus the product being inspected is critical to achieve optimum performance. With the center of the metal detector being the least sensitive, the closer the product is to the wall of the metal detector, the higher its sensitivity and chances of detecting a contaminant. Sensitivity is reduced when the aperture is too large compared to the actual product.
- Risk Location. To determine the best place to put a metal detector on a production line, an audit will show where along the line the greatest risk of metal contamination might occur and so installation most beneficial.
- Sourced Materials. One of the most common sources of metal contamination is when the raw food product arrives at the processing plant, as contamination can occur during the preparation / harvesting of the materials or during transportation to the plant. Taking this into consideration will help you determine where the most effective place is to inspect.
- Metal Types. As part of the audit, when determining the source of a metal contaminant, find out what type of metal it is. Metal detectors respond differently to ferrous, non-ferrous and stainless steel, but all are very standard to detect with today’s X-ray inspection systems. Of the three metal types, stainless steel can be the hardest to detect as it comes in various grades meaning some are magnetic and others completely non-magnetic with poor conductivity making detection relatively hard, so it is best to check for stainless steel as part of your regular performance validations.
- Maintenance. It is critical all equipment along the production line is regularly maintained to a high standard, as a common source of metal contamination is from process machinery wear or failure resulting from machinery damage. For example, blades for chopping or mixing when damaged could result in metal fragmentation.
- Hindering Factors. There are other factors that can hinder the detection of metals, such as when a product is wet or contains a high salt content that creates a high product signal. Most metal detectors can be adjusted to manage these factors accordingly and ensure optimum detection. The orientation of the contaminant, such as a piece of wire can also cause issues.
- Metal Free Zone. If you have not heard of the term Metal Free Zone (MFZ) then you need to know about it. The MFZ is an area surrounding the aperture of a metal detector that should be kept free of any fixed or moving metal. The area is sensitive and if you place metal too close to a metal detector, (i.e. in the MFZ) the signal will spike, leading to false rejects.
- Testing. When installed, you need to ensure regular testing to verify detection to the required levels. Loma metal detectors make this easy as the integral PVS (Performance Validation System) instructs you to pass test packs through the detector at pre-set intervals.
Share This Post:
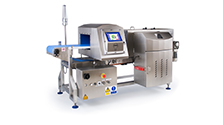
Reliable Detection with Loma's IQ4 Metal Detector's
The IQ4 series of Metal Detectors include many features designed to aid uptime and productivity, including revolutionary variable frequency technology that optimize detection levels around a wide range of differing product conditions.
If you need more information contact us on 01252 893 300 or request expert advice
If you need some advice, please feel free to call us or request an expert, click the button and fill out the form.
We have a UK based customer service team ready to help and keep your food safe.